 |
 |
 |
 |

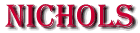





 |
 |
 |
 |
 Since 1966 I have been doing glassblowing and
making ornamental specialty items. My type of glassblowing is called
"Lampworking." The other kind is called "Off Hand" and is where you take raw
glass from a furnace. I use rods and tubes to create what I need. I hope you
will consider purchasing some of these items as it also helps support this
website!
 |
 |
 |
 |
 |
 A Standard
Annealing
 I am no expert on
anything having to do with glassblowing or lampworking, but have learned a few
of the simple things. I looked for many answers on the internet and only found
a few vague (to me) references having to do with many things...especially
annealing glass.
 Usually even the rawest beginner knows that glass
that is uneven in temperature will crack and glass that has been heated in a
particular area and then not cooled properly, is in serious jeopardy of
cracking. Let it cool and then go back and re-heat it and it will probably
crack. So the way to solve these problems is to get an annealing oven (or kiln
or lehr).
 I have had an annealing oven for about 35 years, my former one
being an analog version. At first I had an analog pyrometer (the thingy that
tells you the temperature), but soon enough got a digital one. You can still
buy them on the internet.
 Finally I got a digital annealing oven. I have a
Paragon (see: www.ParagonWeb.com) F130. My former one was a Paragon and I have
found these people to make the finest quality you will ever see and have the
best support you will ever find! Love them to pieces! For my purposes (and
budget) the F130 is all I currently need. You can program it, stick your
beautiful creation into it, punch it on and go to bed and get it out in the
morning.
 So..............after all of that jabber, here are a few hints
on how to properly anneal your glass. Excuse me, but I only use Corning 7740
Pyrex® because I am pretty lazy and it works very well. Soft glass (COE
103) will crack more easily than the "borosilicates" (COE 33). These
suggestions are if you are annealing a piece that is already at room
temperature. If the piece is really hot, then pre-heat the oven to at least 950
and start, but the piece has to be uniformly hot or you might crack it. The
same thing works in reverse. If you are going to seal something to a piece you
are working on, it is good if you have already pre-heated it at about 1040
degrees F so that it will already be hot when you take it out of the oven. Make
sure that the piece you are working on is really hot when you seal it
on.
 FIRST: The rule of thumb is that for every quarter inch
of thickness, you need to anneal the piece for an hour. (Some people might say
30 minutes, but I am conservative.) There is a lot of latitude in small pieces,
for many small pieces don't have enough stress in them to even need annealing,
but it would always be more beneficial.
 SECOND: The "STRAIN" point of
Pyrex® is 950F whereas for the other borosilicates it is 960F. So spend
your life's savings on a good oven like mine and program it to go up to about
970F for the first ramp. And set it to FULL BLAST if your piece is "robust" and
is not likely to shock and you're starting out a room temperature. Why? Because
we need to get there in a hurry so that the glass is now "safe" from any
cracking. (If your work is already HOT, then have the oven already warmed up.)
But why the 970F? Because the controller is not accurate enough, nor the
firebricks thoroughly hot enough to properly hold a high temperature
yetand when it gets to that temperature, you're naturally going to have
the controller hold it there for about 10 minutes, so that all of the glass can
become the same temperature (at the strain point)...AND...when it starts
"soaking," the temperature will drop as much as 18 degrees or so. But since the
strain point is 950, we don't really care. It will still be safe. IF...you've
already made an object, and it is quite hot, then try your best to get the
entire piece about the same temperature throughout and then pop it into the
oven at about 950F because we don't want to cool it down if it is already
hot.
 THIRD: For your next "ramp" you are going to want to go
all of the way to the proper target temperature for annealing. For my
Pyrex® it is 1040F. Now here's where it gets a little tricky. You may have
thin glass on your piece and you don't want it to SLUMP and thereby become
distorted, so since Pyrex® starts slumping at about 1050F, then stay away
from there. Here's how you can easily do it.
 FOURTH: This time when we raise the
temperature from our previous 970F to 1040F we lower the speed by which it
achieves that temperature (ramp speed) to about 140, which means that it raises
the temperature 140F per hour. In other words...SLOWLY. You can go as high as
200. By letting it ramp up slowly, then you let the firebricks get a uniform
temperature throughout and the whole oven will achieve uniformity. You will
want to set your "soak" period to at least an hour or more. I just made a
dolphin that was an inch and a half thick, so I set it for 6 hours. Holy Cow!
That seems like a long time, but failure is much more lasting! If you gaze at
the temperature like I sometimes do, then you will find that the temperature
will probably only rise to about 1043F at most, which is still SEVEN DEGREES
below the slumping point. Gradually the temperature will go back down to 1040F
or even a little lower, but soon it will become very steady at almost exactly
1040F. For the full "soak" time.
 FIFTH: Now we have annealed our piece and want
it to all cool down. BE PATIENT!!! The more slowly you cool it all down, then
the less stress there will be in the glass (cannot be overemphasized!!!). Do
something else for awhile. But program your controller for a series of steps
(in temperature) DOWN from 1040F. Use a slow speed like about 200-300 so that
the oven won't cool down quickly, for the "slower the better." Go down to about
1020F and hold for about 20-30 minutes. Then go down to your 970F again and
hold for about another twenty minutes. Keep the speed SLOW! Then go down to
about 920F. Hold for about 15 minutes. By holding, the oven is forced to really
slow down. Now we are BELOW the strain point, so stress might be induced, so we
are going to go slowly. Then go down to about 800F and have a speed of about
200. Hold for about 20 minutes. Then go down to about 600F and hold for about
10 minutes. After that, you are safe. Pyrex® has a shock point of about
350F, which means that if it is cooled about 350F really quickly, you could be
in trouble. But your room has a temperature of probably at least 70F, so if
your oven is at 400F, then even if you took the piece out, it would probably be
safe. Don't do this. Leave it in the oven. But the point is, that your
annealing cycle should be OVER. Wait until it has cooled down to within 50F of
room temperature if you have to, but I prefer to let it cool all of the way
down to room temperature, so that I can open the door and simply pick it up
with my hand. You know...the hand with all of the burn scars. But seriously,
the more patient you are, the better it will go. Many artists cool as long as
they anneal, so get it in your head that you're not in any hurry if you want
genuine success.
 One of the nice things about properly annealing your
glass piece is that after it is completely cool, if you made any mistakes in
creating it, you can usually (if you're careful and warm the area slowly!) fix
the mistake. Bad joints can be more properly sealed by using a tiny pinpoint
flame for a full, proper seal. If a seal has visible strain marks or is cloudy,
it is a bad seal. If you boiled the glass and have too many bubbles in it, it
is also a bad joint. A "cloudy" joint is a bad joint. If you can see where the
glass is joined to the other piece of glass, then it is a bad joint. A good
joint just flows into the other piece of glass. Experienced people will pull
off a bad piece like that with a pair of tweezers. Naturally, after repairing
(especially for a crack), then you have to run it through the firing cycle all
over again, but that's the price of excellence.
 I'm sure some of
you experts have differing ideas on this, but I was just vain enough to want to
put something on the internet about this subject because I was so frustrated by
not being able to find out the proper information on my own. I had to do it
"trial-and-error" which is the surest method, but also the slowest. If you have
better suggestions, then send them to me and you can "school" me and I will
thank you.
 The "SOFT" glasses will have a much lower set of temperatures,
but since I don't use them, then you will have to look them up
yourself.
 REMEMBER: Annealing is about 70% science and 80% ART! The best
of Blessings to you. If you're in a hurry to get your glassware out of the
oven, you might consider another hobby. Success is much more sweet than
failure. Also, if you have to make any last minute adjustments, like repairing
a sudden crack, it will be easier to do with a very small flame and your work
already annealed.
 Last suggestion: Don't drop it when you take it out of the oven.
I've done that! Other suggestion, (to me especially) put the hot end of the
glass away from you and quit forgetting which tool you have just used in the
flame and don't pick it up or touch the hot part. When you burn yourself, get
it cold quickly and for the next week, run cold water over the wound for about
5 minutes at least 6 times a day. I was a hospital corpsman in the Navy and
know that you can cure nearly any wound if you can just keep it REALLY CLEAN.
This doesn't mean you can put the standard ointments and dressings on it, but
at least 6 times a day, let clean cold water just flow over it to clean the
wound. Now that you're really depressed you can get back to your glassblowing
shop.
 As Harry Truman said, "If you can't stand the heat, then get out
of the kitchen."
 Mike says, "The chances of you getting burned in
glassblowing are 100%, so organize your tools, think a little and minimize your
risks. Then write me and complain that I didn't warn you enough. Then also
write me and tell me of your successes. I had no teachers, so if a knucklehead
like me can do it, then so can you.
 Tricky Work
 There
are pices in flameworking that require a delicate touch to annealing. One of
them is a grand piano. The problem with pianos and ships and butterflies, when
you do loop stitching as I do, is that you wind up either having an area get
cold or you have thinner glass upon thicker glass.
 Well, here's how
I overcome that. Cracks in your work are really not acceptible, and are usually
caused by uneven cooling. If you use borosilicate like I do, then the glass
cools very quickly and has a narrower time that you can use it. Furnace workers
stick their piece back in the oven and it is called "Flashing the Work." We
can't do that, so that primary method of overcoming that problem is to try and
use as much of the flame as possible and keep the whole area around which you
are working the same heat. But after the piece gets to a certain size, there is
another way. If you have a digital oven like I do, then you can set at about
1010 degrees Fahrenheit (roughly) and when you have made as many stitches as
you think it's going to get dangerous, then open the oven or a bead door and
stick it in the oven. Wait until the temperature gets back to your "garaging"
temperature and then take the piece out and add some more. With a piano, it's
extremely difficult because it gets heavy directly proportional to its size. I
build a 3-point holder out of 7 mm rod which will be connecting to the 3 legs.
I bend my end of the rod 180 degrees upon itself so that I can have a better
grasp of whether or not the work swvels in my hand. Make sure these connections
on your work frame are very good. You might anneal them because you are
probably going to be using this frame again.
 To make a piano, I make the three legs
first. and ram them quickly into vermiculite so that they will stay somewhat
warm. Then I make the frame of the piano. The straight sides are easy enough,
but on a grand piano, it has an ogive that is basically curved like a snake a
little. The trick to keeping out "bumps" on this is to make VERY slow curves
and take your time. Once you finish making the frame and are satisfied that
nobody's going to laugh at you, then attach the legs to the corners of the
frame. Seal them very well, because they themselves are in danger of cracking.
Flame anneal them very well. Then take your 3-pointed holding frame and attach
it to the 3 legs of the piano. Make the legs longer than you need so that you
will not have to go back and add more glass. Now you have the frame and the
legs. This is a good time to attach the pedals, for your glass should already
be somewhat hot. Gradually raise that area's temperature and seal an area
behind the keyboard. (This is my technique.) After sealing about a half-inch
running area, then pull off another three quarters of an inch towards the back
of the piano's rear. We're inside the box of the piano now. After you have
added the legs and pedals, attach a stabilizing rod between the back of the
pedal area up to that piece we put just behind the frame itself. Be sure to
keep this area very warm at all times. Now you are finished with the basic look
of the piano. I put on the pedals, for you will never get a better
chance.
 Then immediately stick it all in the oven. Your oven is around
1010 degrees, so let's switch over to a proper annealing routine of ramps and
holds and properly anneal the frame and the holding rod. I have a bead door, so
I can let the frame rod partially hang out the bottom of the bead door with it
mostly closed. Anneal it for at least 3 hours. Once you do this, then you are
completely free to start on the frame with your loop stitches and do them a
section at a time as previously mentioned so that the frame doesn't crack. Keep
repeating this process. It's slow work, but better than getting cracks. If you
are lightning fast at making loops, then you may not need to do this, for all
of your areas will still be hot, but I am slow. Once you finish the piano's
box, then lace it up with strongs and anneal the whole thing again. After
annealing, then you can put the lid on at a 45 degree angle and also add the
lid support to hold it up there. It's almost impossible to seal it to the lid
without cracking the lid, so I wait until the whole piece is finished and then
add a drop of ultra-violet glue (which is clear) and seal that end of the lid
suppoting rod. Back to the work. After you have added a lid, then anneal it all
again. Now, except for the legs, we are finished. Burn the legs off of the
frame we have created and make the piano sit properly and you're done. Anneal
it again and you really are finished. While you're waiting for the piano to get
to the annealing temperature, you can make a piano bench or stool and simply
stick it in with the piano. The size of the piano is only dictated by how much
you can handle. It's very tiring to be holding something that keeps weighing
more and more at arm's length. Also, only so much will fit into the oven. Good
luck and let me know if there is a better way. |
 |
 |
 |
|
 |
 |
 |

|
|